Csepel Power Plant - Concrete production from recycled glass
We strategically address the principle of sustainable development and use environmentally friendly technologies. For this reason, G.M.I Engineering has commissioned us to produce a high-performance, heat-insulating concrete for the bottom of the 80,000-litre tank at the Alpiq power plant in Csepel, which will be used to store hot water (instead of gas oil).
The tank will no longer be able to store gas oil, but 95-degree water, so a material with excellent thermal insulation properties was needed. This is why recycled glass was chosen.
The bottom plate of the tank is in direct contact with a material that cannot withstand the thermal stress coming from the hot water temperature. As a solution to this technical problem, the main contractor came up with the idea of using lightweight insulating concrete.
Product features
During production, the glass is sorted, crushed, ground and finally sieved. The granules are produced in a high-temperature kiln at around 900 degrees Celsius. At the end of the process, the fine porous granules are obtained, which are sieved after cooling, then sorted into several fractions and finally filled into bags.
The foam glass granules used inhibit the flow of heat, as the granular structure traps air, thus providing a thermal insulation effect. The foam glass is also highly heat resistant and fully resistant to organic and inorganic chemicals, except hydrogen fluoride.
What makes it environmentally friendly?
Foam glass is one of the most widely used thermal insulation materials in green architecture. It is important that the foam glass does not contain toxic substances. Glass waste used as a raw material provides an excellent energy balance through recycling, as it is harmless to living organisms, can be produced with a low energy investment and can be recycled almost indefinitely
Sustainable cement production
Our company strives to minimise the use of raw materials and energy in cement and concrete production by exploring opportunities to substitute natural minerals.
We also provide heat for the kilns in the Vác and Beremend Cement plants with sustainability in mind. The heat demand for clinker production is met primarily by using fuels from alternative sources, which have now become essentially the primary fuel for the cement industry.
Location
Színesfém utca 11211 Budapest (Hungary)
Csepeli Erőmű.
Duna-Dráva Cement Kft.
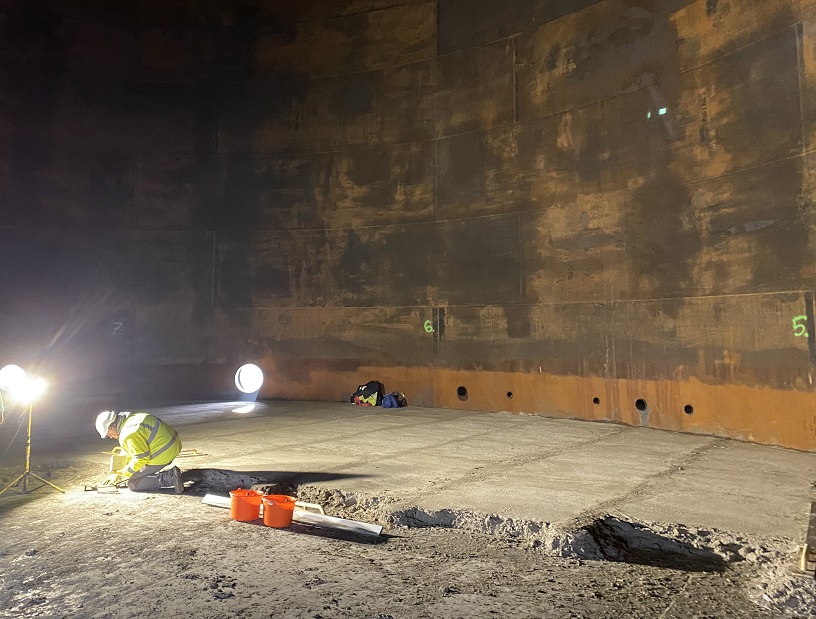
Csepeli Erőmű.
Duna-Dráva Cement Kft.
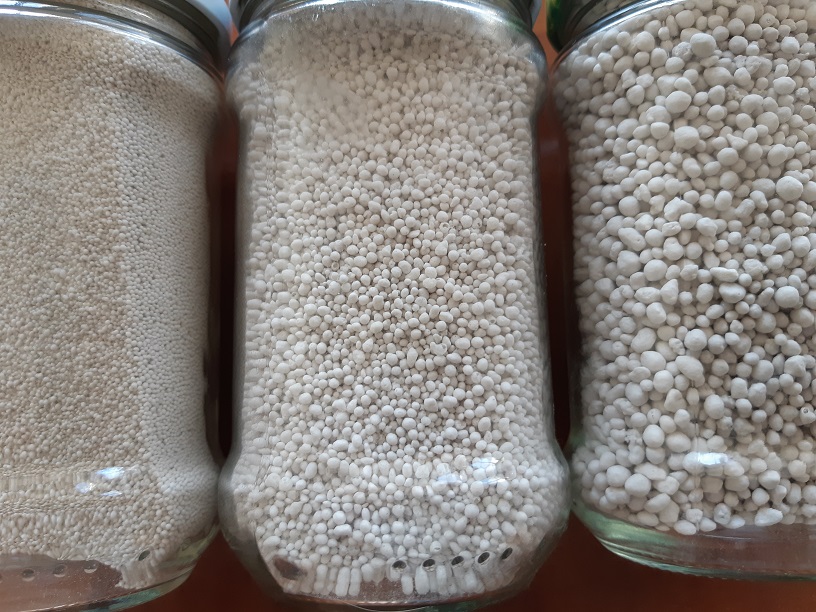
Csepeli Erőmű.
Duna-Dráva Cement Kft.
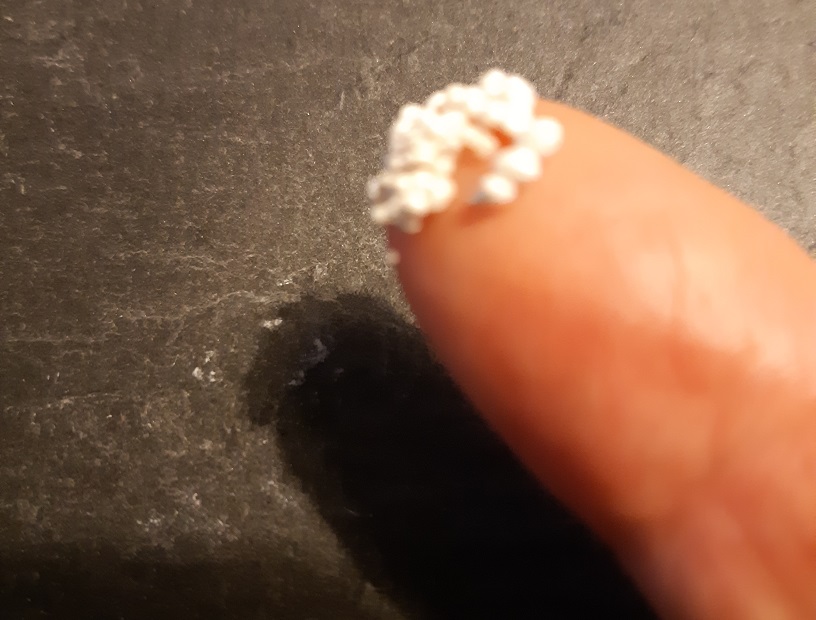
Csepeli Erőmű.
Duna-Dráva Cement Kft.
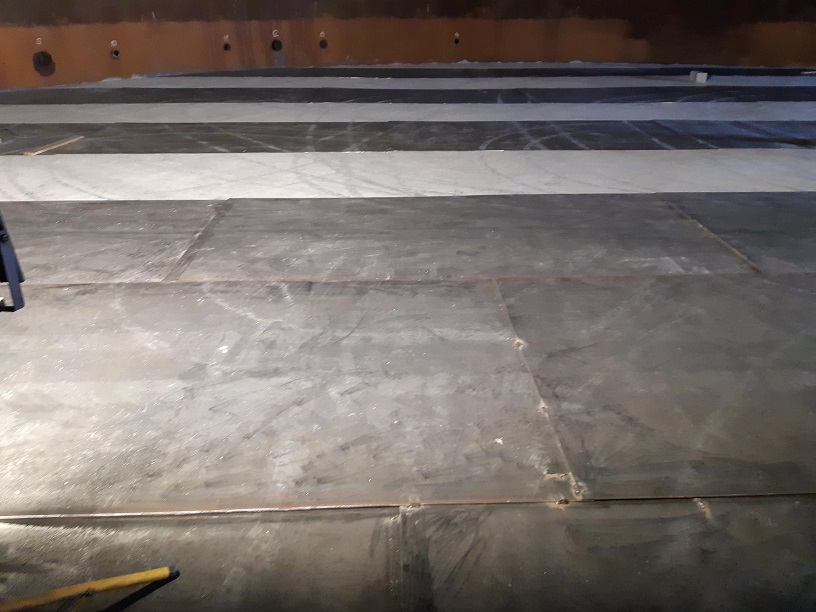
Csepeli Erőmű.
Duna-Dráva Cement Kft.
Csepeli Erőmű.
Duna-Dráva Cement Kft.
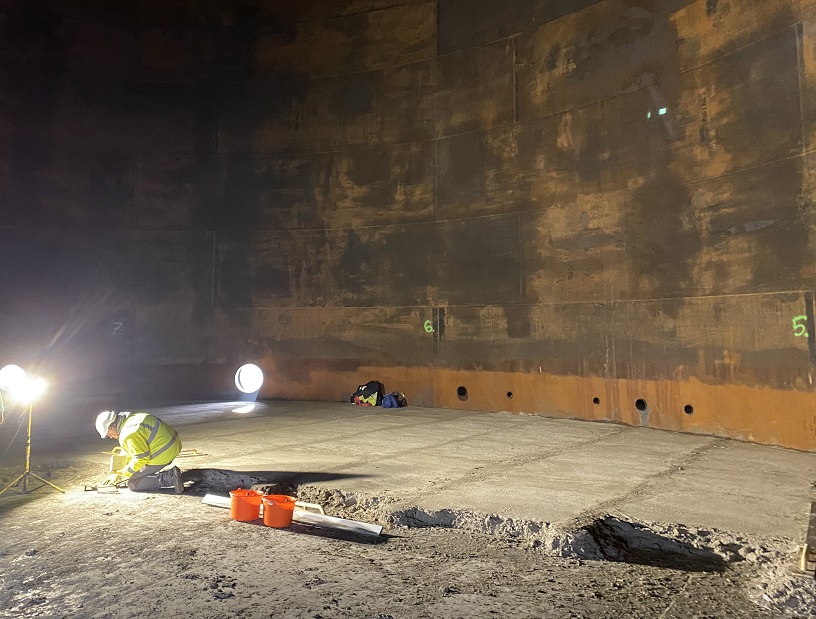
Csepeli Erőmű.
Duna-Dráva Cement Kft.
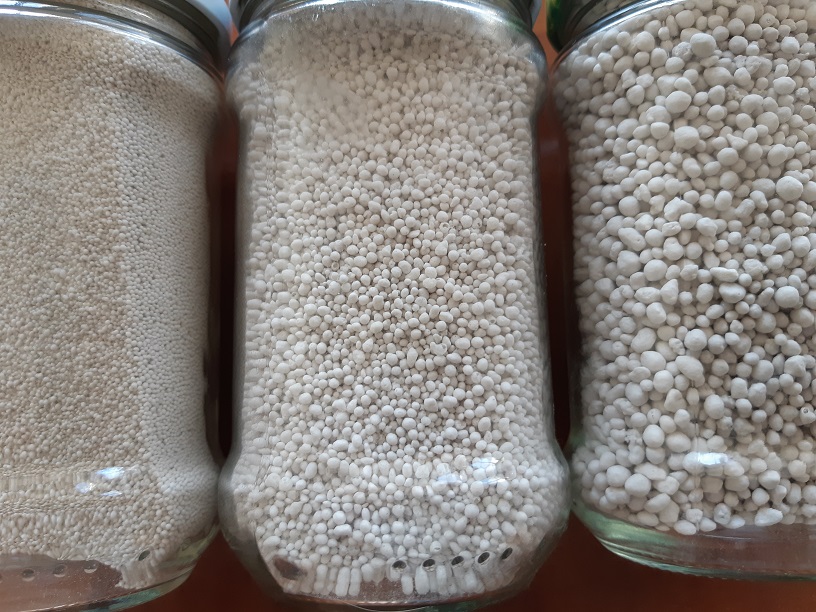
Csepeli Erőmű.
Duna-Dráva Cement Kft.
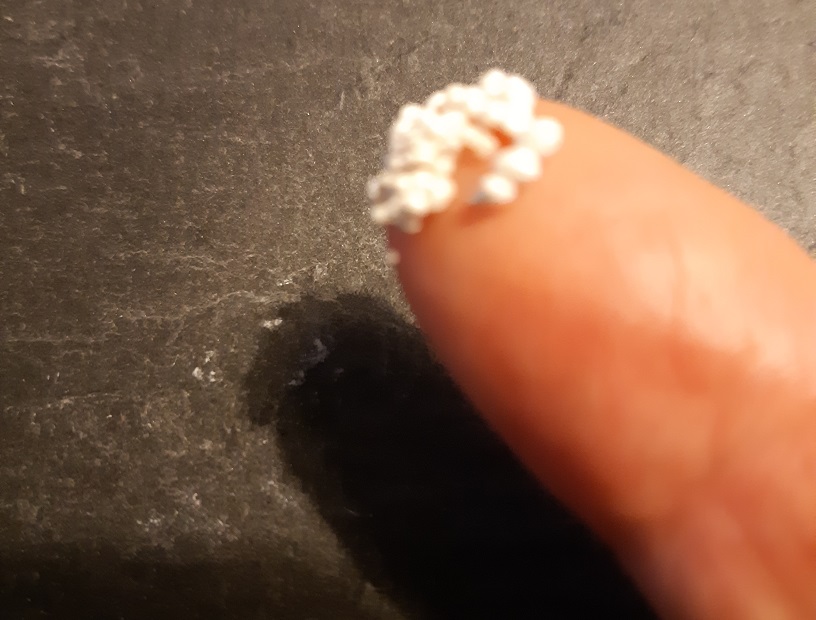
Csepeli Erőmű.
Duna-Dráva Cement Kft.
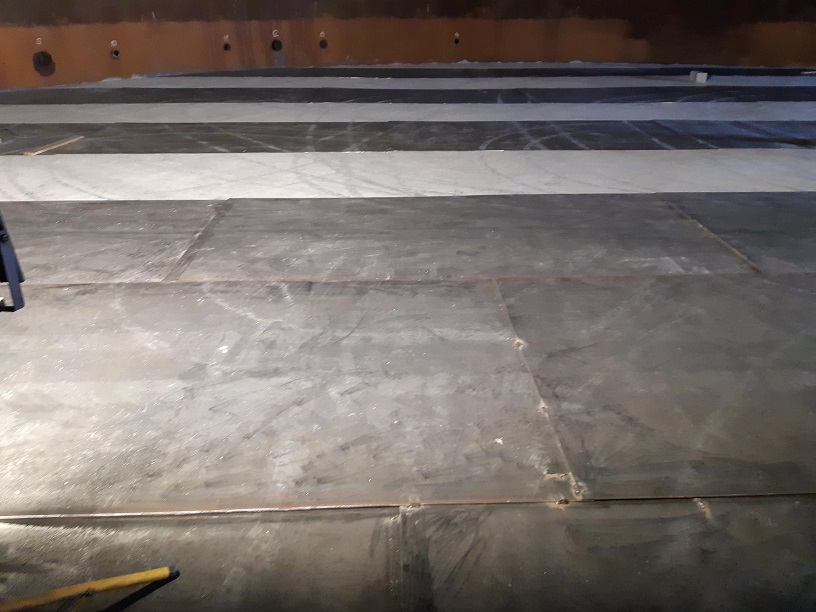
Csepeli Erőmű.
Duna-Dráva Cement Kft.